computational kinetics group
kinetic methods . fundamental transport processes . multi-scale, multi-physics systems
research activities
hybrid continuum/kinetic solver for chemically reacting flows
combined kinetic approach for DSMC rare events and tail-driven processes
assessment of continuum breakdown in high-speed chemically reacting flows
exploiting the role of defects for enhanced thermoelectric material performance
calibration of DSMC parameters for transport processes in ionized air based on ab initio calculations
The computational kinetics group employs DSMC, deterministic Boltzmann methods and MD to explore and improve modeling for engineering systems ranging from high-altitude, rarefied flows to material modification and material response through irradiation processing.
Some of our current research activities include:






DSMC study of carbon fiber oxidation in ablative thermal protection systems

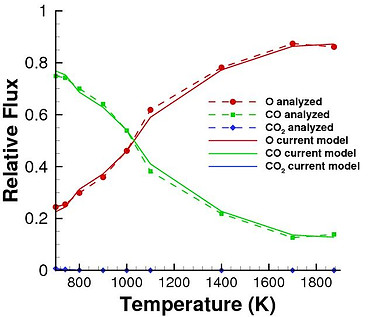

Carbon based ablators are commonly used as thermal protection system (TPS) materials in hypersonic atmospheric entry missions to shield space vehicles from extreme heating. During Earth re-entry the TPS is exposed to the partially dissociated atmospheric gases in which atomic oxygen (O) is the most reactive with carbon surfaces. Interaction with these gases alters the surface of the vehicle and modifies the chemical composition within the boundary layer. Thus, precise knowledge of the gas-surface interactions and the chemical reactions at the surface is critical for accurate modeling of the ablation process and prediction of heat loads.
The aim of this work is to develop a finite-rate surface chemistry model for the oxidation of preform carbon ablators. Molecular beam experiments performed using a hyperthermal beam on vitreous carbon is studied and analyzed using direct simulation Monte Carlo (DSMC). A detailed surface chemistry model for carbon-oxidation is developed that reproduces all the observed experimental data. This model is then applied to all the fibers of preform and validated against molecular beam experiments on preform carbon.
DSMC study of carbon fiber oxidation in ablative thermal protection systems
We gratefully acknowledge funding for this research provided by the National Science Foundation, NASA, AFOSR, DOE, Air Force Research Laboratory and the University of Illinois at Urbana-Champaign.
Computational resources and technical support are provided by NASA through the High-End Computing Capability (HECC) and by DOE through the PSAAP Center.





